10 Useful Tips to Help You with Tinning Wires
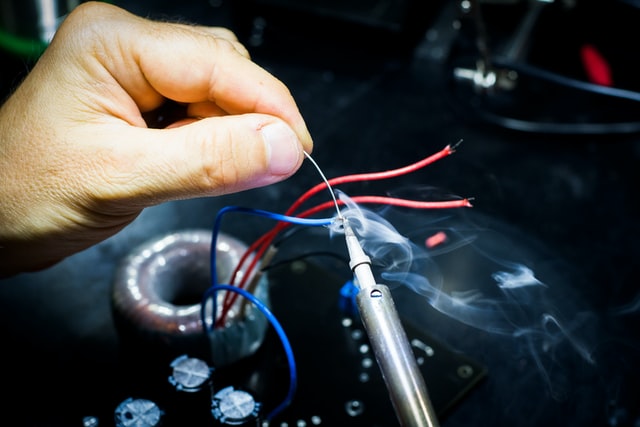
Whether you are preparing a circuit board, doing automotive electrical work, or splicing a line in your home wiring as a jumper, you have probably dealt with the irritation of fraying wires that just won’t cooperate.
At Bob’s Handyman Company we know it is more common with certain gauges and materials, but even so, it is still enough to make you pull your hair out.
The solution is a simple concept called tinning. It is the process of adding a metallic, highly conductive compound to the point where the wire is frayed so the wire strands are all melded together.
Tinning Your Wires
Every good or bad electrician knows that tinning copper wires is common in electrical work where substandard wiring is used. When the wires are stripped it begins unravelling almost immediately. Braiding it into another wire, then feeding both into a wire nut, becomes an exercise in futility. Tinning with solder that coats the end of the wiring before it frays stems the hassles.
It is a great idea for wiring outlets or switches. These have screws that hold the wires in place, providing current. Tinning wires for screw terminals are the easiest way to have an easy to work with wire end. This process is easy and saves time.
The standard way to tin wire is with your best soldering iron, using flux and silver solder. Once the strands have been banded together, they are much more manageable.
Tinning flux
For the most efficient tinning, using flux speeds up the soldering process tremendously. You might be asking “what’s tinning flux?” It is a soldering component that is a conductive jell which distributes heat across the entire area being soldered, instead of just one small area. The rapid heat transfer helps to spread the solder over the length without much effort.
Tinning without flux is what most people know when they think of soldering. A needle or cone tip on a soldering iron, heating silver solder, then dripping the molten liquid onto the item to be bonded. For circuit boards and items of a similar delicate nature, flux is not to be used. If doing it for electrical work, flux is a great thing to have on hand.
Tips for Effective Wiring
The best way to dive in is to get yourself a tinning kit, which most often consists of a soldering iron, silver solder spool, a metal container of flux, wire strippers, and a sponge for cleaning your iron tip. These tips will show you how the tinning of components is done.
- Use acid-free, rosin-core solder, also known as electrical-grade solder. This will have the purity percentage that will allow for the best current flow after the wire is tinned. The rosin-core is made up of flux.
- Tinning a wire for soldering can only be done to a bare wire. Strip it before you get started prepping everything else.
- Clean the tip of your soldering gun. Plug it in, heat it up, and wipe the tip on a sponge, getting off the residue leftover from previous work.
- When applying the solder, make it clean without bubbles. The molten silver will want to drip. Applying intermittent heat instead of constant heat will prevent that.
- Always let the wire cool before you put down your tools and call the job a success. You may have missed a spot. A clean tinning is important.
- Use thin-tipped pliers to bend the tinned wire into a hook shape if attaching it to a screw terminal. Lineman pliers are too fat and square.
- Your soldering iron is extremely hot. Return it to a heat-resistant holder when not using it. It will burn whatever it touches.
- The same principles apply to single-strand and multi-strand wires.
- After your wire is ready, snip off the tip so you have a clean end.
- Never solder the hooked wire onto the screw terminal once attached and screwed down. It will be a huge pain if you ever need to change the outlet or switch in the future.
Other applications
Tinning and soldering can be used in plenty of ways when you need to connect wires.
Creating a jumper from a current-bearing wire in your car to a new component you are adding aftermarket is best done this way. Like adding new stereo equipment or running lights. It is easy to accomplish with this simple trick.
The Why of It All
You have the answer to “how does tinning work?”
Perhaps now we can elaborate on why it is necessary. And the biggest reason is efficiency. Electrical work is hard sometimes, so don’t hesitate to hire a qualified electrician, especially when the materials are being uncooperative, comments Progress Abms. And when you have to put outlets and switches in a building that might have dozens if not hundreds, it can drive you nuts.
It is a way to shorten the process by prepping the wires for maximum speed in install. Put the pre-tinned hook end into the screw terminal, tighten, crew it into the conduit box, and move on.
Easy, clean, no muss, no fuss. And the silver solder delivers a clean current.
Conclusion
For anyone in the electrical field, automotive field, or home theatre niche, if you don’t use this process, I hope you will not. It seems like an extra step, but ultimately, it will make the work faster and your life easier. Have you ever had to tin a wire?
For help, Bob’s handyman company is expanding to areas outside Greater London. We are now covering the following NWK areas:
Leave a Reply